Modernisierung bei laufendem Betrieb:Anlagenrealität und Dokumentation im Einklang
Prozess- und verfahrenstechnische Anlagen sind meist jahrzehntelang in Betrieb. In dieser Zeit sind Modernisierungsarbeiten unerlässlich. Während des laufenden Betriebs die entsprechenden Maßnahmen durchzuführen ist vor allem dann schwierig, wenn die Prozessleittechnik in die Jahre kommt und deshalb modernisiert oder gar komplett erneuert werden soll. Erfahrung und Kompetenz aller Beteiligten sowie eine gute Planung und Vorbereitung sind dann der Schlüssel zum Erfolg. Eine wichtige Voraussetzung liefert in diesem Zusammenhang ein leistungsfähiges Dokumentationswerkzeug, das Daten aller in der Anlagentechnik vorkommenden Quellen verarbeiten kann und nicht nur während der Modernisierung, sondern auch während des Betriebs praxisgerechte Nutzungsmöglichkeiten bietet.
Der Schwerpunkt der deutschen Erdgasproduktion liegt in Niedersachsen. Erdgas ist immer eine Mischung aus Methan und verschiedenen anderen Gasen, wie Kohlendioxid, Stickstoff, höheren Kohlenwasserstoffen und in manchen Lagerstätten auch Schwefelwasserstoff in unterschiedlichen Konzentrationen. In Norddeutschland ist das der Fall. Da Schwefelwasserstoff nicht nur übel riechend, sondern auch sehr korrosiv und giftig ist, wird Erdgas deshalb, bevor man es nutzt, in Aufbereitungsanlagen „gewaschen“. Die Prozessleittechnik einer solchen Anlage wurde jetzt in einem Großprojekt bei laufendem Betrieb umfassend modernisiert.
Spezialisten arbeiten Hand in Hand
Einen wichtigen Teil der Erneuerung bildeten dabei die Restrukturierung und das Neuaufsetzen der gesamten Dokumentation für die Mess-, Steuer- und Regeltechnik. Dazu galt es bereits vorhandene Daten entsprechend einzupflegen, neue Quellen zu integrieren und die sich in der Modernisierungsphase immer wieder ergebenden Änderungen ebenfalls in die „lebendige“ Dokumentation zu übernehmen.
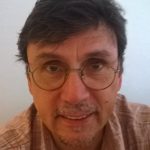
Bild: Honeywell
Verantwortlich für die Modernisierung der Erdgasreinigungsanlage waren Spezialisten für industrielle Prozesstechnik aus dem Hause Honeywell Deutschland. „Als Partner für die Erarbeitung der Dokumentation holten wir uns bereits zu einem frühen Zeitpunkt die Karlsruher Firma Rösberg ins Boot“, erläutert Torsten Wildgrube, Projektleiter bei Honeywell. „Ursprünglich war die Anlage ja mit dem PLT-CAE-System ProDOK der Karlsruher geplant worden. Das kam uns zugute, da wir uns aus logistischen und kommerziellen Gründen bei der Vor-Ort-Dokumentation bereits für LiveDOK entschieden hatten, das aus dem gleichen Hause stammt. Von der intensiven Zusammenarbeit mit Rösberg hat letztendlich dann das gesamte Projekt ganz erheblich profitiert.“
Phasen der Dokumentation
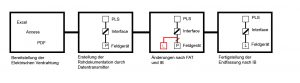
Bild: Rösberg/Honeywell
Die Dokumentation durchlief dabei unterschiedliche Phasen: das Erfassen vorhandener „alter“ Daten, die Erstellung einer Rohdokumentation, die Übernahme aller aktuellen Änderungen nach dem Funktionstest der einzelnen Anlagenteile und schließlich das Fertigstellen der Endfassung nach der Inbetriebnahme. Zuerst musste also die vorhandene Verdrahtung in aktueller Form zur Verfügung gestellt werden. Die Dokumentationsspezialisten arbeiteten daraufhin alle Planungsunterlagen wie Kabellisten, Klemmlisten, Feldgeräteinformationen und PLS-Informationen in einem im Vorfeld abgestimmten Format auf. Diese PDF-, Excel- und Access-Files wurden dann über den ProDOK-internen Datentransmitter in nahezu fertige ProDOK-Stromlaufpläne importiert. Nach kleineren manuellen Anpassungen entstand so eine Rohfassung der Dokumentation, die dann vor Ort zur Verfügung stand.
„Nun kam der Nutzungsschwerpunkt von LiveDOK“, berichtet Wildgrube, „Die in der Rohfassung fertig geplante und dokumentierte Anlage war jetzt den reichhaltigen und nachträglichen Änderungen unterworfen, die sich in größeren Projekten zwangsläufig immer einstellen. Zusätzlich mussten Signalwege skizziert werden, die nicht einfach importiert werden konnten, da sie zu komplex waren für die normale Importroutine, aber zu gering im Vorkommen, als dass es sich gelohnt hätte, selbige anzupassen.“ Hierfür bietet das elektronische Dokumentationssystem LiveDOK, das speziell für die Prozesse und Belange der Betriebsbetreuung entwickelt wurde, ideale Voraussetzungen.
Offen für alle Aufgaben, schnell und intuitiv zu bedienen
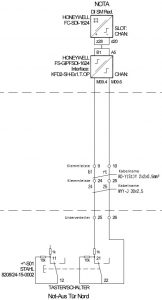
Bild: Rösberg/Honeywell
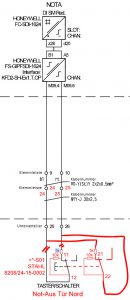
Bild: Rösberg/Honeywell
LiveDOK begleitet den kompletten Lebenszyklus der Dokumentation, beginnend bei der Erstellung über die komfortable Benutzung bis hin zur Revision der geänderten Dokumente. Dafür sorgt das „Herz“ der Dokumentationssoftware, der leistungsfähige LiveDOK-Generator, der für nahezu alle denkbaren Aufgaben offen ist. Er verarbeitet alle gängigen Formate, kann also Grundrisse, Lagepläne, Verfahrensfließbilder und PLT-Stellenlisten ebenso managen wie Bedienvorschriften, Prüfanforderungen und Wartungsanleitungen.
Auch für Änderungen gibt es unterschiedliche Möglichkeiten. Die Redlining-Palette beispielsweise reicht von Handschrifteingabe über Markieren, Durchstreichen und vielem mehr bis hin zu dynamischen Stempeln. Auch eher spezielle Aufgabenstellungen lassen sich auf diese Weise effektiv und komfortabel lösen.
Nachträgliche Änderungen leicht gemacht
„Für eine Abschaltung war zum Planungszeitpunkt noch nicht eindeutig bekannt, welche Anforderungen letztendlich umgesetzt werden sollten“, berichtet Wildgrube. „Es konnte jedoch die Grundfunktionalität erstellt und als Rohfassung dokumentiert werden. Die während des FAT (Factory Acceptance Test, also der Funktionsprüfung vor Ort) festgelegte Vorgehensweise zur Anbindung des Feldes an das Signal, wurde dann mit LiveDOK dokumentiert und kontinuierlich gewartet, bis die abschließende Dokumentation nach der Inbetriebnahme erstellt werden konnte.“ Auch dass nicht immer die Details zu allen Feldgeräten sofort ersichtlich oder entsprechend kommuniziert wurden erwies sich als unproblematisch. Fehlende Informationen wurden nachträglich im Zuge der Signalprüfung zusammengetragen und in LiveDOK eingepflegt, wo sie in Kombination mit den Ursprungsdaten für eine vorerst vollständige und richtige Dokumentation sorgten.
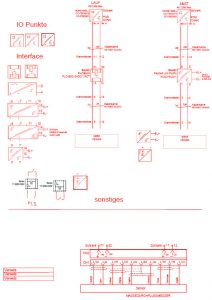
Bild: Rösberg/Honeywell
„Als Bonbon bei der die Bearbeitung von komplexeren Loops entpuppte sich die Möglichkeit, Zeichnungen und Screenshots per Copy-Paste-Verfahren in die Dokumentation zu übernehmen“, führt Wildgrube weiter aus. „Mit diesem Werkzeug ließen sich alle zum Loop gehörenden Informationen beilegen, die für die fertige Zeichnung wichtig und interessant waren. Als Spielart dazu wurden Roteinträge komplexerer Natur gelegentlich mit Bitmaps ergänzt.“ Gelegentlich war es auch erforderlich, artgleiche Einträge auf mehreren Loops möglichst effizient einzutragen. Diese konnten per Suchfunktion gesucht und dann schnell überschrieben werden. Mit Hilfe von Templates und Typicals ließen sich neue Loops vergleichsweise schnell erstellen und vorhandene umarbeiten, in dem der entsprechende Eintrag einfach kopiert wurde. „Die Bearbeitung glich so manchmal dem einfachen Zusammenschieben von benötigten Einzelteilen“, freut sich Wildgrube. Insgesamt waren für das Projekt mehr als 7.000 Loops zu bearbeiten, mehr als 12.000 I/O-Punkte wurden angeschlossen und natürlich galt es auch noch viele weitere Dokumente zu verwalten, zum Beispiel für die mehr als 200 Schaltschränke.
Im laufenden Betrieb lässt sich natürlich genauso gut von der elektronischen Anlagendokumentation profitieren. Als „Real Time As-Built Documentation“ stellt das System alle Informationen in Echtzeit zur Verfügung. „Die Anlagendokumentation entspricht damit immer dem realen Zustand der gebauten Anlage“, so Wildgrube abschließend. Alle Beteiligten haben immer Zugriff auf die aktuellsten Informationen; Änderungen sind schnell und einfach gemacht und obendrein auch jederzeit nachverfolgbar. Die Dokumentation kann mit jedem beliebigen Rechner mit Webbrowser eingesehen werden.
Titelbild: Rösberg