High-Performance HMI - mehr Effizienz im BetriebGute Prozessbilder sind „langweilig“
Bei PLS-Prozessbildern haben fehlende Richtlinien zur Bildgestaltung und immer leistungsfähigere Grafikprogramme zu einer verstärkten Unübersichtlichkeit geführt. Animationen zahlreicher Details, bunte 3-D-Darstellungen, drehende Rührer, sich kreuzende Leitungen etc. sind zwar hübsch anzusehen, helfen dem Bediener aber nicht unbedingt weiter. Stattdessen geht schnell der Überblick über den Gesamtprozess verloren, abnormale Prozesszustände oder Alarmmeldungen werden zu spät erkannt bzw. im schlimmsten Fall sogar komplett übersehen. Gute Prozessbilder sollten deshalb auf grafische Überfrachtung verzichten und sich stattdessen aufs Wesentliche konzentrieren. Hier können moderne High-Performance HMIs mittlerweile Maßstäbe setzen. Sie bieten informationsorientierte Darstellungen der Prozessdaten, steigern das Situationsbewusstsein des Bedienpersonals und unterstützen so einen proaktiven und damit effizienteren Anlagenbetrieb.
Am Anfang der Darstellung komplexer Prozesse standen die guten alten Messtafeln, die im Hinblick auf Übersichtlichkeit einiges zu bieten hatten. So lieferten sie nicht zuletzt durch eine apparatebezogene Anordnung der Anzeigen einen guten Überblick über den Gesamtprozess. Status- und Trendanzeigen erleichterten es schon damals dem Bediener, den Anlagenzustand auf einen Blick zu erkennen. Die Funktionalität dieser Lösung war naturgemäß jedoch eingeschränkt. Hier versuchten die ersten rechnergestützten Prozessbilder Abhilfe zu schaffen. Da jedoch Richtlinien oder gar Standards zur Bildgestaltung fehlten, führten immer leistungsfähigere Grafikprogramme zu immer unübersichtlicheren Prozessbildern. Letztendlich gab es zwar viele Daten, aber wenig Information. Die Darstellung nicht wirklich relevanter Details rückte in den Vordergrund, Farben wurden nicht konsistent eingesetzt.
Schlechte Prozessbilder fördern schlechte Bedienpraktiken
Inzwischen hat sich gezeigt, dass solche „Prozessbilder“ ganz wesentlich zu Anlagenstörungen beitragen können. Animationen wie drehende Rührer oder Ventile, farblich codierte Rohrleitungen, die fast schon plastische Darstellung von Behälterfüllständen oder leuchtenden Farben für alle Anzeigen sind grafisch anspruchsvoll, lebendig und schön anzusehen. Den Bediener lenken sie jedoch durch die ungenügende Strukturierung, eine meist eingeschränkte Bildnavigation oder den kompletten Verzicht auf Trends und analoge Darstellungsweisen von den wesentlichen Informationen ab. Er kann „vor lauter Bäumen den Wald nicht mehr sehen“.
Solche nicht optimalen, aber weit verbreiteten Prozessbilder, die bei eher unwichtigen Details zu übertriebener Animation greifen, fördern leider auch schlechte Bedienpraktiken. Bei dem ganzen bunten Treiben gewöhnt man sich schnell daran, erst auf „richtige“ Alarmmeldungen zu reagieren bzw. das Alarmsystem als Bedienermeldesystem zu missbrauchen. Dieses „Operating by Alarms“ steht allerdings im krassen Gegensatz zu einem proaktiven Anlagenbetrieb, bei dem der Bediener aufgrund der ihm sichtbaren Prozessinformationen schon im Vorfeld einer Störung eingreifen kann. Kritische Anlagenzustände können so vermieden werden, was dann natürlich die Effizienz des gesamten Prozesses erhöht.
Gute Prozessbilder erhöhen das Situationsbewusstsein
Genau dies setzen sich High-Performance HMIs als Ziel. Sie wollen dem Bediener ein besseres Situationsbewusstsein vermitteln, sodass er abnormale Anlagenzustände erkennen kann, bevor ein Alarm erzeugt wird. Genauso wichtig ist dann das schnelle Erfassen von Alarmen, ein besserer Überblick über den zu bedienenden Prozessteil und nicht zuletzt auch die Berücksichtigung gesundheitlicher Aspekte. Das Design ist so zu wählen, dass es ergonomisch ist und dafür sorgt, dass die Konzentration des Bedieners auch über lange Zeiträume nicht nachlässt. Wichtige Grundlagen dafür, an denen sich z.B. die Automatisierungsspezialisten der M+W Process Automation GmbH bei der Prozess-Visualisierung orientieren, liefert heute das High-Performance HMI Handbook (PAS) sowie die Normen und Richtlinien des VDI, der NAMUR, ASM und ISA bezüglich Bildschirmarbeitsplätzen und Gestaltung von Prozessbildern.
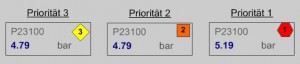
Auf den ersten Blick sehen entsprechende Prozessbilder dann zwar „langweilig“ aus, weil sie mit Farbe sparsam umgehen und auf überflüssige Animationen verzichten. Schaut man genauer hin, wird schnell deutlich, dass der Informationsgehalt und vor allem die Informationsqualität hoch sind. Ein ganz wesentlicher Punkt ist dabei der Einsatz von Farbe. Farbe erzeugt Aufmerksamkeit, deshalb funktionieren gute Prozessbilder ohne übertriebenen Farbeinsatz und heben nur abnormale Zustände farblich hervor. Dabei bewährt sich vor allem bei Alarmmeldungen eine redundante Codierung von Farbe, Form und Text sowie ein spezielles Objekt für den Alarmzustand. Bei Statusanzeigen orientieren sich gute Prozessbilder am „Glühbirnenprinzip“. Heller als der Bildschirmhintergrund signalisiert dann „Ein/Auf/Läuft“, dunkler steht für „Aus/Zu/Steht“.
Bildobjekte mit schnell verwertbaren Informationen
Gleichzeitig werden relevante Daten in einen Kontextbezug gestellt, denn nur dann werden sie zu einer verwertbaren Information. So ist die heute oft übliche Kolonnendarstellung von Messwerten nur mit viel Fachwissen im Hinterkopf zu bewerten. Wesentlich einfacher wird die Bewertung der Messwerte, wenn gleichzeitig der Normalbereich dargestellt ist oder sogar noch eine dynamische Analoganzeige hinzukommt. Das erlaubt auch dem Nichtspezialisten die schnelle und eindeutige Bewertung der Messwerte.
Gerade solche Analoganzeigen kommen dem menschlichen Sehen, das auf die Mustererkennung ausgelegt ist, sehr entgegen. Ähnliches gilt auch für Spinnendiagramme, die eine kompakte Informationsdarstellung auf kleinem Raum ermöglichen oder Trendanzeigen, die eindeutig darüber Aufschluss geben, wann eingegriffen werden muss. Grundlage dafür ist eine sinnvolle, voreingestellte und im Bedarfsfall eventuell auch veränderbare Zeitbasis sowie deutlich erkennbare Gutbereiche und Alarmgrenzen. Gleichzeitig sollte die Darstellung eine geeignete Autoskalierung haben.
Vom „Big Picture“ bis zum Diagnosebild
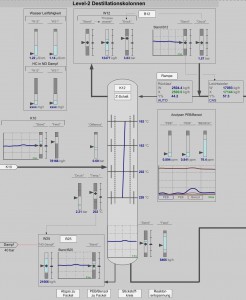
Bei einem guten High-Performance HMI sorgen klar strukturierte Hierarchieebenen zudem dafür, dass dem Bediener keine überflüssigen, sondern immer genau die Informationen zur Verfügung stehen, die er braucht. Das Prozessübersichtsbild zeigt deshalb den vom jeweiligen Bediener zu überwachenden Anlagenteil und lässt ein schnelles Erfassen des Gesamtzustandes zu. Die nächste Ebene ist das Prozessbedienbild. Es bildet das mentale Prozessmodell des Bedieners ab; ein Großteil aller Bedienhandlungen ist von hier aus durchführbar.
Muss der Bediener mehr ins Detail gehen, z.B. für eine Fehleranalyse oder um nicht routinemäßige Eingriffe vorzunehmen, unterstützen ihn dann die Prozessdetailbilder. Die höchste Detaildichte aller aktuellen Prozessinformationen findet er schließlich auf den Prozessunterstützungs- und Diagnosebildern. Hier lassen sich u.a. Standarddisplays für einzelne Messstellen darstellen und auch zusätzliche Informationen integrieren, z.B. Verfahrensanweisungen, Bedienerhilfen etc. Bei einer solchen Struktur ist es dann ein Leichtes ganz nach Bedarf immer tiefer in den Prozess „einzutauchen“.
Die Effizienzsteigerung ist nachgewiesen
Von derart aufgebauten High-Performance HMIs profitieren Anlagenbetreiber in der gesamten Prozessindustrie. Sie verbessern durch die übersichtliche Darstellung das Situationsbewusstsein; der Bediener kann schneller reagieren, und das oft schon, bevor ein Alarm ausgelöst wird. Störungen lassen sich auf diese Weise schneller beseitigen und nach einer Störung wird eine schnellere Rückkehr in den Normalbetrieb möglich. Dies bestätigen z.B. auch einschlägige Studien. Laut einer ASM-Untersuchung (*) lassen sich abnormale Zustände mit High-Performance HMIs bis zu fünfmal schneller erkennen als mit konventionellen Lösungen. Die Erfolgsrate bei der Handhabung dieser Zustände liegt 37 % höher. Der Zeitaufwand für ihre Beseitigung sinkt im Schnitt um 41 %, also fast auf die Hälfte. Die Folge davon ist ein deutlich effizienterer Anlagenbetrieb. In einer Ethylenanlage beispielsweise ergab sich auf diese Weise ein jährliches Einsparpotential von etwa 800.000 US Dollar.
Alle Bilder: M+W / PAS