Großer Durchsatz bei hoher PräzisionAntriebstechnik für Mikroelektronik-Fertigung
Im digitalen Zeitalter liefert Mikroelektronik die Grundlage für Innovationen. In vielen Branchen ist sie die Basis für neue leistungsfähige Produkte und Dienstleistungen, angefangen von Maschinenbau und Fahrzeugtechnik bis hin zu Medizintechnik oder künstlicher Intelligenz. Von der Kaffeemaschine bis zum Kommunikationssatelliten gibt es fast nichts mehr, was ohne Mikrochips funktioniert. Damit ist die Herstellung mikroelektronischer Bauteile zur Schlüsseltechnologie geworden, die wiederum hohe Anforderungen an die eingesetzten Komponenten hat. Die Massenproduktion verlangt hohe Durchsatzraten bei den automatisieren Abläufen, gleichzeitig aber auch höchste Präzision und das in allen Produktionsschritten bis hin zur Qualitätskontrolle. Kleine, leistungsfähige Antriebssysteme liefern dafür die Voraussetzungen.
Der Grundstoff für die Chipherstellung ist Quarzsand. Aus ihm wird das Silicium gewonnen, das dann über verschiedene Reinigungsverfahren hochrein aufgeschmolzen wird. Ein sogenannter Impfkristall leitet in der flüssigen Masse dann das Kristallwachstum ein. Es entstehen zylinderförmige Stäbe mit homogener Struktur, aus denen Scheiben von etwa zwei Millimeter Stärke geschnitten werden. Diese rohen Wafer werden geglättet, poliert und mit einem lichtempfindlichen Lack beschichtet. Mit fotolithografischen Verfahren sowie Dotierungs- und Ätzprozessen entstehen dann die Leiterbahnen, deren Breite im Nanometerbereich liegen kann. Dazu wird jede Einheit auf dem Wafer in der Regel mindestens 30-mal mit unterschiedlichen Fotomasken belichtet. Die Einheiten müssen dafür jedes Mal präzise ausgerichtet werden, damit sie sich bei jeder Belichtung exakt in der gleichen Position befinden. In diesem vielstufigen Prozess entstehen dann die charakteristischen Halbleiterstrukturen auf der runden Scheibe, der ihr die Ähnlichkeit mit einer Waffel und den Namen verleihen.
DC-, Schritt- oder Piezomotoren für die präzise Positionierung
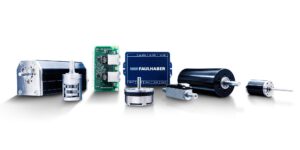
Das Handling der Wafer während dieser Produktionsschritte übernehmen Roboter, die sehr feinfühlig arbeiten müssen, damit die hochempfindlichen Rohlinge nicht beschädigt und präzise ausgerichtet werden, um fehlerfreie Strukturen zu erhalten. Das gleiche gilt für die optischen Komponenten der Laser in den fotolithographischen Systemen. In beiden Bereichen sorgen oft Antriebssysteme von FAULHABER dafür, dass die einzelnen Bewegungsabläufe mit verlässlicher Reproduzierbarkeit gefahren werden. Je nach Applikationsanforderungen kommen dabei entweder DC-, Schritt- oder Piezomotoren mit den darauf abgestimmten Controllern und Getrieben zum Einsatz.
Die Piezo LEGS-Motoren sind mit Auflösungen bis in den Nanometerbereich sehr präzise bei kurzen Reaktionszeiten, arbeiten rastmomentfrei und sind wahlweise als Dreh- oder Linearmotor erhältlich. Typische Einsatzbereiche finden sich beispielsweise bei der Positionierung optischer Komponenten. Die PRECIstep-Schrittmotoren sind durch ihren robusten Aufbau, den großen Drehzahlbereich und die hohe Leistungsdichte auch unter schwierigsten Einsatzbedingungen eine ideale Lösung für anspruchsvolle Positionieraufgaben. Schrittmotoren der Baureihe AM0820 beispielsweise haben das bereits im Weltraum bewiesen: in einem Seismometer, das Marsbeben aufzeichnet.
Bei DC-Motoren, die in der Chipproduktion eingesetzt werden, reicht das Spektrum von 4-poligen Servomotoren für hohe Drehmomente über hocheffiziente Flachmotoren bis zu kleinsten bürstenlosen DC-Mikromotoren. Aufgrund ihres Designs sind die Klein- und Kleinstantriebe prädestiniert für Hochleistungs-Servoanwendungen mit häufigen Überlastbedingungen sowie für Anwendungen im Dauerbetrieb, bei denen eine maximale Lebensdauer erforderlich ist.
Verguss und Test
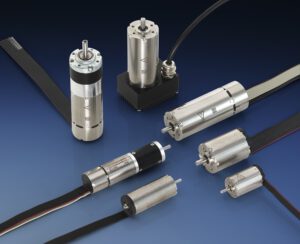
Eine typische Anwendung für die DC-Kleinstantriebe findet sich in den Dosiereinheiten der Maschinen, die dafür sorgen, dass die fertigen Chips ihre schützende Hülle erhalten. Der Vorgang ähnelt dem Kunststoff-Spritzguss, nur dass hier sehr hohe Präzision gefragt ist. Die Menge des Kunstharzes muss präzise dosiert werden, damit der Schaltkreis wirksam geschützt ist. Gleichzeitig darf aber nichts überstehen und Einbau oder Funktion behindern.
Das meist schwarze Kunstharz läuft durch eine Spindel, deren Drehbewegung es in Richtung Spritzgussform befördert. Nach einer genau bemessenen Strecke im Millimeterbereich schaltet der Kleinstantrieb in den Rückwärtsgang, damit sich eine präzise definierte Menge des Harzes ablösen kann und in die Form gelangt. Der Chip ist jetzt fertig und wird im sogenannten Test-Handler geprüft. In dieser Maschine ist ein Pick & Place-Roboter für das Befördern und Platzieren der Chips in den Testvorrichtungen zuständig. Da hier Teile getestet werden, die höchstens einige Quadratzentimeter messen, sind die Dimensionen der Anlagenteile entsprechend filigran. Die Motoren für ihre Bewegung müssen deshalb ebenfalls sehr kompakt sein, zugleich aber sehr hohe Anforderungen an die Dynamik erfüllen und sich natürlich präzise regeln lassen. In sehr vielen Maschinen dieses Prozessbereichs finden sich die FAULHABER-Motoren aus den Baureihen BX4 mit integriertem Motion Controller oder aus dem Portfolio an linearen DC-Servomotoren.
Schnelle Bestückung und Nadelprobe
Die geprüften Chips werden meist in Kunststoffgurte verpackt und gelangen zur nächsten Etappe in der Mikroelektronik-Fertigung: zur Bestückung der Leiterplatten. Auch hier herrscht Massenproduktion, unzählige Komponenten werden täglich auf Millionen von Leiterplatten befestigt. Diese Arbeit übernehmen Bestückungsautomaten. Die Gurte mit den Bauteilen werden auf Rollen der Bestückung zugeführt und so abgerollt, dass der Bestückkopf immer ein Bauteil aufnehmen kann. Letzteres geschieht in der Regel durch Unterdruck: Die Komponente wird angesaugt und auf diese Weise festgehalten. Der Kopf fährt dann an die Stelle der Leiterplatte, an der sich die passenden Aussparungen für die Anschlüsse des Chips oder eines anderen Bauteils befinden. Darauf platziert er die Chips, später werden sie mit der Platte verlötet.
Präzision ist beim Bestücken ebenfalls oberste Pflicht, damit die feinen Anschlüsse nicht beschädigt und exakt positioniert werden. Zugleich braucht man aber großen Durchsatz für die riesigen Stückzahlen. Manche Maschinen schaffen über 100.000 Bauelemente pro Stunde. Hier können die Kleinstantriebe ihre Stärken ebenso ausspielen wie bei der anschließenden Qualitätskontrolle. Die vollautomatischen Testmaschinen müssen ebenfalls einen großen Durchsatz ermöglichen. Die Bewegung der Test-Nadeln etwa ist oft so schnell, dass man sie nur in Superzeitlupe verfolgen kann. Die Antriebssysteme aus Schönaich tragen damit in allen Produktionsschritten zum Erfolg der Mikroelektronik bei.